
Tube & Pipe Welding
Whether its stainless steel or mild steel we are capable of pipe welding to the highest of standards. We are also very proficient at meeting sanitary finishes for the food and beverage industries.
Tube and pipe welding are specialized welding processes used to join cylindrical metal components, namely tubes and pipes, together to create a continuous, leak-tight, and structurally sound connection. These processes are essential in various industries, including construction, manufacturing, oil and gas, automotive, and aerospace, where tubular structures are commonly used.
​
Here are the key aspects of tube and pipe welding:
​
Tube vs. Pipe:
-
Tube: Tubes are generally characterized by their precise dimensions, including outer diameter (OD), inner diameter (ID), and wall thickness. They are often used for structural purposes and fluid transportation.
-
Pipe: Pipes are typically used to transport fluids (liquids and gases) and are categorized by their nominal pipe size (NPS), which is a dimensionless number representing the approximate inside diameter. Pipe schedules denote the wall thickness.
​
​
Welding Methods:
-
Tungsten Inert Gas (TIG) Welding: TIG welding, also known as GTAW (Gas Tungsten Arc Welding), is a precise method suitable for welding thin-wall tubes and pipes. It uses a non-consumable tungsten electrode and an inert gas (usually argon) to create the weld. TIG welding produces clean and high-quality welds, making it ideal for applications where appearance and integrity are critical.
​
-
Shielded Metal Arc Welding (SMAW): SMAW, commonly known as stick welding, is used for heavy-wall pipe welding in outdoor and industrial environments. It involves an electrode coated with flux that creates a protective slag, shielding the weld pool.
-
Gas Metal Arc Welding (GMAW): GMAW, or MIG welding, employs a consumable wire electrode and a shielding gas to create the weld. It is suitable for welding pipes with thicker walls and is known for its efficiency and versatility.
-
Flux-Cored Arc Welding (FCAW): FCAW uses a tubular electrode with flux inside, eliminating the need for external shielding gas. It's often used in heavy-duty applications and in outdoor environments.
-
Submerged Arc Welding (SAW): SAW is used for welding thick-walled pipes and is known for its high deposition rates. It involves burying the arc and weld pool under a layer of granular flux.
​
​
Applications:
-
Tube and pipe welding are used in various settings, including residential homes, commercial buildings, public infrastructure, and industrial facilities.
-
Common applications include the construction of pipelines for the transportation of oil, gas, and water, as well as the fabrication of structural components, handrails, supports, and exhaust systems in the automotive and aerospace industries.
​
​
Quality and Inspection:
-
Tube and pipe welding must adhere to strict quality standards, as defects can lead to leaks, structural weaknesses, or safety hazards.
-
Non-destructive testing (NDT) methods, such as radiographic testing and ultrasonic testing, are often employed to inspect welds for defects without damaging the material.
​
​
In summary, tube and pipe welding are specialized welding processes used to join cylindrical metal components, and they play a vital role in various industries, ensuring the integrity and reliability of tubular structures and fluid transportation systems. The choice of welding method depends on factors such as material thickness, application, and desired quality standards.
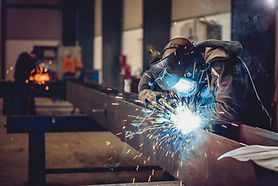

